
When the air flows through it, it will do work on the air and increase the flow rate of the air. The passage between the blades on the working impeller is expanded. The impeller is generally a part of a centrifugal compressor. The programs for machining impeller airfoils were developed with HECTRAN, which is a proprietary processor for impeller machining programs. 5-Axis Milling Titanium/Aluminum Alloy Blade Blisk Used for Aircraft Engines, Find Details about Impeller Blisk, Titanium Impeller Blisk from 5-Axis Milling. Precision CNC Machining Titanium Impeller Blisk for Aerospace. The programs which supply positioning information to this control for machining blisk airfoils were developed with APT and special programming techniques that were devised for these programs. for one section of the blisk/impeller and. China 5-Axis Milling Titanium/Aluminum Alloy Blade Blisk Used for Aircraft Engines, Find details about China Impeller Blisk, Titanium Impeller Blisk from 5-Axis Milling Titanium/Aluminum Alloy Blade Blisk Used for Aircraft Engines - HK AA Industrial Co., Limited. Currently, the integral impeller and blisk are extensively used in military and commercial aircraft engines, e.g., F120, F414, EJ200, and PW600, and in the rst two stages of the high-pressure compressor of a mil- itary engine in China 3, 4. This machine is directed by advanced computer numerical control. and impellers for aero-engines, turbo- machinery and power generation. A new milling machine was designed for this process, which machines four identical parts simultaneously.
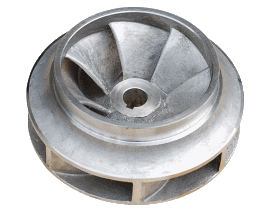
Five-axis precision contour milling was developed to machine the airfoils of the five axial flow blisk stages and the impeller, all of which are integral with their supporting disk. Blisk machining for RC turbine Hi all, I have a blisk that I created for a small (RC-sized) turbine, and am attempting to figure out if fusion360 can come up with appropriate toolpaths.
#Impeller blisk manual#
Processes which were previously available, and which were used to produce airfoils for development engines, were too costly and too dependent on manual skill to meet volume production requirements. This development was carried out under a Manufacturing Methods and Technology contract awarded by the Army Aviation System Command, which later became the Army Aviation Research and Development Command AVRADCOM, to the Aircraft Engines Business Group of the General Electric Company in Lynn, Massachusetts. Highly automated processes were developed to machine and control the quality of airfoils on the blisks and impeller which are the principal rotating components of the compressor for the T700-GE-700 engine, which powers advanced military helicopters.
